数字孪生系统如何帮助汽车制造企业重塑工厂管理
2025-04-29
工业数字孪生解决方案基于虚拟现实技术,制造现场建立基于物联网技术的“智能感知”系统,改造升级现有智能化系统,建立全制造过程可视化集成控制中心,实现对加工设备、机器人、物流设备、仓储等的全面支持。
一、数字孪生系统-实时监控功能介绍
数字孪生系统实时监控技术是定义生产数据与仿真模型之间的映射关系,生产系统根据条件触发向仿真平台发送实时指令,三维仿真平台解析该指令,驱动模型矩阵的变化,实现三维模型的运动。
实时数据驱动物理与虚拟工厂动作同步,搭配便捷巡视和全方位监控,有效提升生产效率、安全性与管理决策水平。这些技术大幅降低人工巡视成本,推动智能制造发展,助力工厂实现高效、绿色、可持续生产。
二、数字孪生系统-实时监控的作用
1、实据虚实同步:实时采集传输数据,实现物理与虚拟工厂同步,精准再现运行状态,保障虚拟环境实时管控。
2、多方式漫游,便捷巡厂:提供多视角、多路径漫游,支持1 / 3人称及自由漫游,助管理人员在虚拟工厂轻松巡厂,全面检查产线与设备状态。
3、全方位监控:利用摄像头、传感器与虚拟现实技术,全方位监控工厂,各环节实时查看管理,及时排查隐患。
4、减员增效,智能巡检:数字化、智能化降人工巡视依赖,省人力成本,提巡视效率与准度借虚拟工厂,管理人员能远程巡查多产区,及时处理问题。
三、数字孪生系统-实时监控的应用价值
1、提高生产效率与安全性:实时同步、全面监控,助管理人员速应设备故障与生产异常,减停机时长、事故率,保生产、护安全。
2、降低成本:精简人员巡视,降低人力成本与培训开支,同步排查问题,减少设备损坏及生产损失。
3、提升决策效率:实时数据和全方位监控为管理层提供精准信息,助力快速科学决策。
4、增强智能制造水平:数字化、智能化推动工厂向智能制造转型,提升技术竞争力,顺应工业4.0趋势。
5、环境友好和可持续发展:减少人员现场巡视,降低设备故障导致的资源浪费、能耗与排放,助力工厂实现绿色可持续生产。
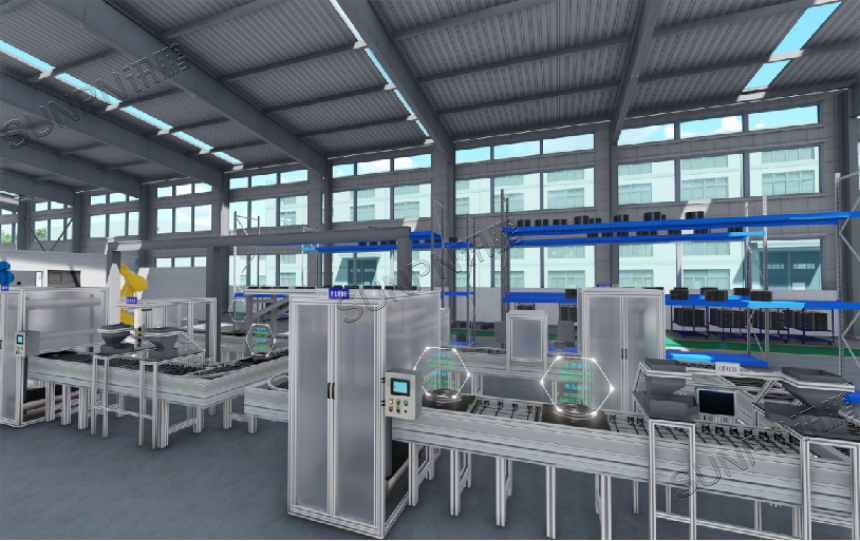
四、数字孪生实时监控技术在某汽车零部件工厂的应用案例
通过先进的3D建模和渲染技术,构建高度还原的虚拟工厂。实现生产设备、产线流程、物流流转的动态展示。结合实时数据采集与数字孪生技术,直观呈现设备运行状态、生产效率、能耗分析等关键指标,支持交互式监控、远程运维和智能优化,提升工厂管理的透明度和决策效率。